Navigating the complexities of data standardization can transform how vessel operators manage their fleets. Data standardization involves creating consistent formats and structures for data, making it easier to share, analyze, and use across different systems and teams. In offshore operations, where there are various systems and technologies in play, ensuring data can be aligned and understood by all parties is key. Whether you’re dealing with legacy systems or new market entrants, setting up an effective data reporting framework is crucial for leveraging industry-wide standards and enhancing operational efficiency.
Many companies manage fleets of 20 to 50 OSVs with small teams and limited technical support. Therefore, solutions need to be turnkey. Providers should demonstrate the business case for digitalization. This should not require major CAPEX investments but deliver immediate efficiency gains and fuel savings.
KEY STEPS
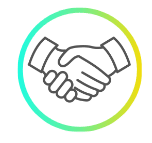
Agree on the desired outcomes: Data Reporting should have clear goals. Engage all levels, from the bridge to boardrooms. Discuss which areas to focus on and improve. Identify where data can provide actionable recommendations and real value.
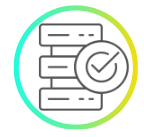
Ensure data quality: Ensure that the data collected is of high quality. This requires the right tools and algorithms for integration. Combine these with monitoring and analysis from human experts, whether in-house or external.
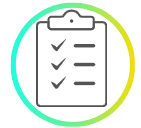
Test in real-life conditions: Implement a trial phase to ensure teams are familiar with new standards. Testing in real-life conditions helps uncover issues and confirms that the system meets operational needs.
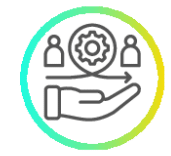
Change management: Change can significantly impact the people involved in the digital transition. They should be included in goal setting and project planning to ensure that everyone is on board with what is to come.
Digitizing noon reports is a practical starting point. These reports provide valuable data on fuel consumption, location, and crew movements. Combine this with engine running hours to gain insights into vessel operations. This data helps identify idle time and areas for improvement.
THE EXAMPLE OF ADNOC L&S
To maximize fuel efficiency for ADNOC L&S, the Opsealog team used daily data to suggest improvements to fleet standby practices. Despite safety policies limiting engine use, we identified significant efficiency gains. Some vessels spent up to 80% of their time in standby mode, requiring at least two main engines running. This high standby fuel consumption was compounded by fuel used to maintain positions at night.
We found that shallow waters with nearby artificial and natural islands created opportunities for installing mooring buoys. By working closely with ADNOC L&S, we implemented these buoys to reduce engine use in dynamic positioning mode. This solution balanced safety with operational efficiency.
The change management and project implementation skills developed by ADNOC L&S become part of their company culture. While demonstrating immediate gains from data standardization, they also build long-term capabilities for adapting to new industry initiatives.
Learn more in our recent interview with Riviera Maritime Media.
DIGITAL MATURITY LEVELS
Opsealog believes that operators’ level of digital maturity will directly impact their readiness for the changes ahead:
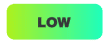
E-reporting may be used for a few reporting functions, but many people in the company rely on manual reporting. Changes in regulations, such as the need to meet EU MRV requirements, will put strain on these people and lead to data redundancy, wasted effort, and confusion.
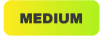
Reasonable progress has been made in adopting data management standards, but some manual reporting remains and systems are not fully interoperable. Meeting new regulatory requirements or corporate KPls will require significant lead time and project coordination.
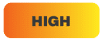
Most reporting functions now operate through digital platforms, ensuring strong data interoperability. Effective data management and security standards are in place. New regulatory requirements or corporate KPIs are implemented smoothly, fostering a culture of innovation. These data standards help transform ambitious ideas into achievable goals, enhancing the company’s reputation and success.
In short, digitalization and regulatory preparedness go hand in hand. Now is the time to act. By building the right digital structure, shipowners and charterers can already analyze their fleet operations and maximize the efficiency of their existing assets to cut greenhouse gas emissions. When the time comes, they will have the insights needed to make informed decisions on retrofits and newbuilds. Data drives evidence-based decision-making and allows each company to chart its practical path toward compliance in a way that aligns with its business goals
MOVING AT DIFFERENT SPEEDS
The OSV sector, much like other commercial shipping sectors, has owners and operators who view the need to decarbonize with various degrees of urgency. Frontrunners have set net-zero operation as a strategic priority within their company. Some have set specific targets and dedicated budgets to achieve them. Others are more likely to adopt solutions only when the immediate value is clear. And some don’t have the resources to assess new technologies, so they wait for regulation to force change.
This gap in ambition drives companies to adopt digitalization at different speeds. It will become a key differentiator going forward. Companies that build a strong digital foundation today will be able to understand their fleet and operations, take action to reduce their emissions, and demonstrate their results, giving them a head start when regulation on GHG emissions comes into force. Meanwhile, those that lag will lack this agility and risk losing their standing in the market as the impact of data standardization currently under development takes hold.
Learn more about it in the White Paper, Creating Value from Data Standardization.