Discover how an Oil & Gas Operator’s Marine Logistics Department leverages Opsealog solutions to optimize fuel consumption, reduce idle time, minimize gas emissions, and streamline cargo and bulk operations.
Context
Our West Africa-based client, operating a fleet of 60 Offshore Support Vessels (OSVs), sought our assistance in enhancing vessel monitoring. They wished to effectively address non-compliance with company procedures and implement necessary corrective measures. The client currently uses Marinsights and Streamlog products to digitize, monitor and improve vessel performance.
The client expressed a specific interest in monitoring fleet efficiency in two key areas: firstly, ensuring adherence to fuel consumption best practices, and secondly, assessing the amount of idle time experienced by vessels while mobilized for specific offshore assets. Additionally, the client desired to identify and present specific optimization opportunities directly to key stakeholders, emphasizing the potential for improvement in these areas.
For example, the client requested the identification of specific vessel activities where improved practices could have resulted in better outcomes. They desired specific data as:
- Start and end time of the activity,
- Operations Location: where activities occurred,
- Number of engines used,
- Manual comments from the crew,
- and any other relevant information necessary to provide a comprehensive context.
This would enable a thorough analysis and understanding of the situation.
Read more: Brunei Shell Petroleum Co. and Opsealog to boost fuel efficiency and optimizing fleet operations
Project
To address the client’s requirements, we established a clear timeline for the project. Opsealog proposed the following steps to ensure efficient and timely delivery:
Day 0: Conduct a 30-minute meeting with the client to gather information and fully understand their objectives.
Day 3: Present a solution proposal to the client, incorporating their specific needs and feedback collected during the meeting. Allow for further discussion and feedback collection from the client.
Day 6: Finalize the solution proposal based on the client’s feedback and ensure its alignment with their objectives. Seek validation and approval from the client for the proposed solution.
Day 7: Implement the approved solution and set it up in a production environment. Configure the system to generate automated reports every week, with reports being received by the client every Thursday.
Proposed Solution
The proposed solution entails the generation of a weekly performance report. This report is automatically sent via email to key stakeholders. This report will highlight the top 10 best and worst practices in various areas related to fleet efficiency. The specific topics covered in the report include:
- Fuel Potential Savings per Activity: The report will identify the potential fuel savings, providing insights into specific fuel consumption optimization actions.
- Idle Time Offshore Asset: It will analyze the unproductive time experienced by vessels while mobilized for offshore assets.
- Gas Emissions: The report will assess gas emissions, highlighting areas where emission reduction measures could be implemented, thereby promoting environmental sustainability.
- Cargo and Bulk Activities per Product: It will analyze cargo and bulk activities, categorizing them based on the type of product being transported. This will help identify any inefficiencies or opportunities for improvement in handling specific products.
- Distance Sailed: The report will also include an analysis of the distance covered by each vessel
Read more: Opsealog ‘Data Democratization’ to Improve Maritime Sustainability
Benefits
- Operational Practice Notifications: The system will notify the relevant stakeholders of any deviations from the company’s standards. This allows for swift action to be taken to address specific issues and communicate with the vessel captain promptly, enabling timely resolution of any non-compliance.
- Facilitating Internal Discussions: The data provided in the reports will serve as valuable information for internal discussions between marine, logistics, and offshore asset teams. Specifically, the focus on decreasing idle time offshore assets can lead to collaborative efforts in optimizing operations and improving overall efficiency.
- Continuous Measurement of Improvement: The weekly reports will enable the client to measure the progress and effectiveness of the implemented practices. By comparing data week after week, it becomes easier to identify trends, track improvements, and gauge the success of initiatives aimed at enhancing vessel performance and adherence to company procedures.
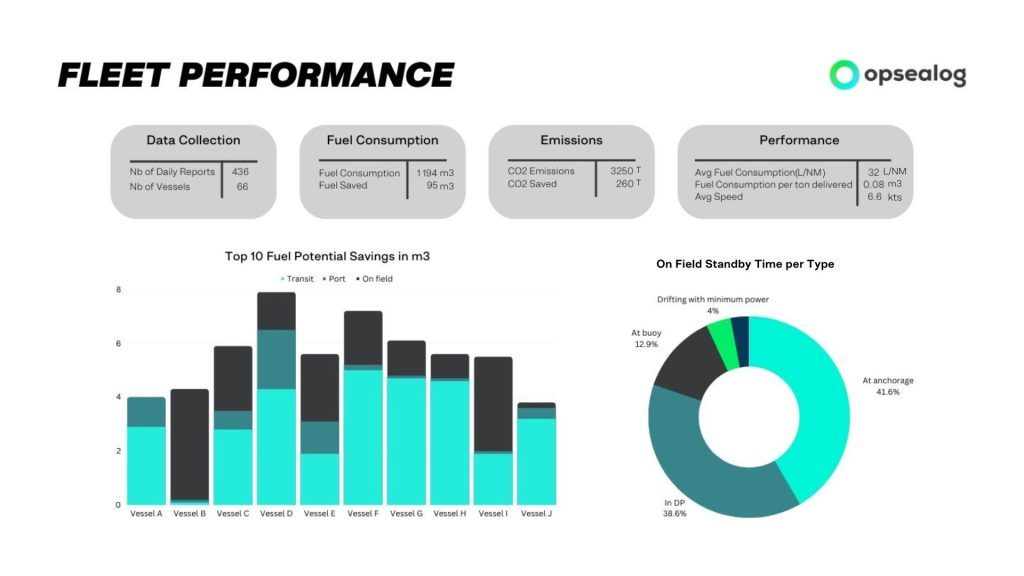
Read more: How to effectively monitor ship fuel consumption without additional sensors
Takeaways
In conclusion, the successful implementation of data collection and analysis in our client’s fleet has brought about significant improvements. By defining key performance indicators, implementing robust data collection, and utilizing advanced analytics, we were able to uncover valuable insights and identify areas for optimization.
This data-driven approach empowered the client to proactively address non-compliance, and track their progress week after week. The generated PDF reports provided actionable information to key stakeholders, enabling them to make informed decisions and drive continuous improvement. Ultimately, this success story demonstrates the power of harnessing data to improve efficiency and reduce costs.