Discover how an Oil & Gas operator from the Middle East leveraged Opsealog’s solutions and achieved fuel consumption savings, minimized GHG emissions, and reduced maintenance requirements by optimizing engine utilization.
Driving Maritime Excellence:
At Opsealog, we’re committed to driving operational excellence in the maritime industry. For instance, our recent collaboration with our client revealed a remarkable case study showcasing the power of data-driven insights and proactive intervention.
Our success at Opsealog lies in our data and maritime expertise. Clients often see us as the ‘eyes’ of their company. Indeed, while data is readily available, uncovering potential issues demands meticulous analysis. To achieve this, our team follows a routine assessment with a structured approach, focusing on three critical operations: in-port standby, on-field standby, and transit.
In addition, by leveraging sistership comparison*, areas for improvement and abnormal behaviors can be identified. In this case, shortly after data collection started, a misbehavior was detected during in-port standby, prompting deeper analysis.
The upcoming section will highlight the tangible outcomes achieved by implementing our best practices.
*A sistership is a vessel virtually identical in design and specifications to another vessel. They are often built in a series with minor variations, simplifying operations and maintenance.
Learn more about different use cases Opsealog’s solution can address
Identifying Deviations in Engine Utilization:
This study was done on a PSV (Platform Supply Vessel). A PSV is a specialized vessel used to support offshore drilling rigs and production platforms. They transport essential equipment, supplies, and consumables. These include cement, baryte, bentonite (dry powders), drill water, liquid mud, methanol, and various chemicals for specialized operations.
Usually, conventional vessels adopt a standard procedure minimizing engine usage while vessels are alongside or at anchorage. However, during a routine assessment, we identified a deviation aboard one of our monitored vessels. Between June and September 2023, the vessel was observed to be using its main engines contrary to standard procedures. As a result, a noteworthy shift in operational behavior became apparent in the following months when observing the average engine utilization patterns.
Aligning Operational Practices for Efficiency:
Upon sharing this observation with the operational team, a review was initiated. By comparing the vessel with its sistership, valuable insights were gained. Adjustments were made to align operational practices with industry standards and best practices.

The results were striking. As a matter of fact, from October 2023 to January 2024, fuel consumption plummeted from a projected 39,988 liters to a mere 18,650 liters. This reduction not only translated into significant cost savings but also led to a remarkable 53% decrease in average fuel consumption. Significantly, this equated to a reduction of 58 tons of CO2 emissions, contributing to our sustainability goals.
Optimizing Engine utilization for Long-Term benefits:
The optimization efforts extended cost and emissions reductions. By optimizing engine utilization, the vessel managed to operate its main engines for 356 hours less, saving 14.8 days of operational time for a single main engine. This not only enhances the vessel’s reliability but also reduces maintenance requirements, leading to long-term operational efficiency gains.
Driving Results through Collaboration:
This use case underscores the transformative power of data-driven insights and collaborative efforts in the maritime sector. Through proactive intervention and continuous improvement, we’re driving tangible results that benefit both our clients and the environment. At Opsealog, we’re proud to be at the forefront of innovation, shaping the future of maritime operations.
This success story exemplifies the industry’s commitment to driving positive change through innovation and collaboration.
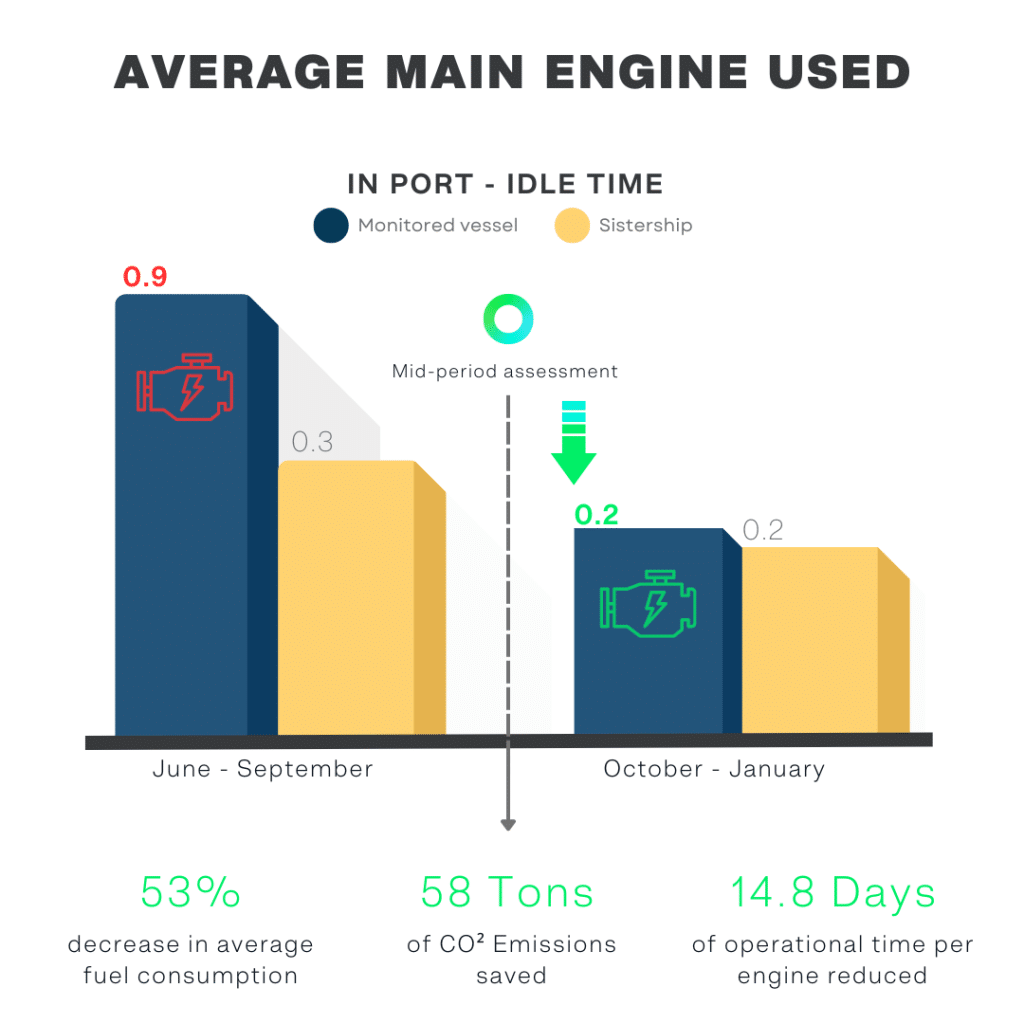