In the competitive world of maritime and oil & gas operations, optimizing fleet performance is essential for reducing costs, enhancing efficiency, and minimizing environmental impact. This blog explores key strategies for fleet optimization, backed by a real-world use case demonstrating the importance of choosing the right offshore supply vessel.
With high fuel prices and daily rates at levels unseen since 2008, charterers are seeing their global costs increase drastically after several years of low costs. This is driving a push towards digital systems that enable them to monitor their operations to improve fuel efficiency in the immediate term and identify the right vessels and fleet size to fulfill their needs in the longer term. In short, for charterers, efficiency is driven by the need to reduce costs as much as possible in a fast-evolving market. In practice, we already see charterers using digital systems to ensure that the right vessel type and size are assigned to the right task and to identify specific needs for the next vessel.
How to Choose the Best Offshore Supply Vessel
Choosing the right Offshore Supply Vessel (OSV) is paramount for achieving efficient, safe, and cost-effective operations in the oil and gas industry. The optimal vessel ensures timely supply deliveries, secure transportation, and minimizing operational costs. This guide provides a thorough approach to selecting the best OSV tailored to your specific needs.
1. Understand your operational needs
Understanding your operational needs and environmental conditions is crucial for selecting the appropriate OSV. Evaluate the major following operational profiles :
- Transits: Frequent movement between ports and offshore installations demands vessels with high fuel efficiency and speed to reduce operational costs. Consider vessels with advanced propulsion systems and fuel-efficient designs to maximize performance.
- Standby Operations: Vessels in standby roles require low fuel consumption during idle periods and robust dynamic positioning (DP) systems to maintain stability near offshore platforms. Opt for vessels equipped with efficient engines and sophisticated DP systems to minimize fuel use and ensure precise positioning.
- Inter-Field Transits: Movement between fields requires versatility and reliability. Vessels should have adaptable cargo capacities and be capable of handling various offshore conditions to support diverse operational tasks.
2. Identify types of Offshore Supply Vessels
Offshore Supply Vessels (OSVs) come in various types, each tailored for specific tasks and conditions. While there are over 12 types, the four most prevalent OSVs in the oil and gas industry are:
- Platform Supply Vessels (PSVs): Represent approximately 40% of the OSV market.
PSVs are designed to transport supplies to and from offshore drilling rigs and platforms. They feature large open decks for cargo, containers, and equipment, as well as below-deck areas for liquids such as drilling mud, fuel, and water.
- Anchor Handling Tug Supply Vessels (AHTS): Account for about 30% of the OSV market.
AHTS vessels are used for anchor setting, rig towing, and various support activities. They are equipped with powerful winches and robust towing capabilities, essential for handling anchors and towing rigs.
- Multipurpose Support Vessels (MPSVs): Comprise roughly 15% of the OSV market.
MPSVs are versatile vessels capable of performing a range of tasks including supply duties, construction support, and ROV operations. They are equipped with advanced technology and equipment to support various offshore activities.
Together, these three types constitute about 85% of the OSV market (MarketsandMarkets) (PBI Research).
3. Evaluate Vessel Specifications
When evaluating vessel specifications, consider the following:
- Cargo Capacity: Ensure the vessel can handle the required cargo volume, including both deck space and under-deck storage. Adequate cargo capacity is vital for efficient supply operations.
- Dynamic Positioning (DP) System: Vessels equipped with DP systems offer enhanced stability and positioning accuracy, essential for precision operations in challenging environments. Ensure the DP system is up-to-date and meets operational requirements.
- Propulsion Systems: Choose the appropriate propulsion system based on operational needs, cost considerations, and environmental regulations. Options include Diesel-mechanical, Diesel-electric, Hybrid, and LNG-fueled systems. Each type offers distinct advantages and suits different operational profiles.
Aligning vessel features with specific operational requirements and environmental conditions will optimize performance and efficiency. Proper evaluation of vessel specifications ensures that your OSV performs reliably and cost-effectively in diverse offshore scenarios.
4. Prioritize Fuel Efficiency
Fuel efficiency is critical for reducing operational costs and minimizing environmental impact. Look for vessels designed with advanced fuel-saving technologies and optimized for efficient fuel consumption to achieve long-term savings and adhere to environmental standards.
5. Assess Technological Integration
Leveraging advanced technology is essential for optimizing operational efficiency and enhancing vessel performance. Consider the following technological features when evaluating Offshore Supply Vessels:
- Real-Time Monitoring Systems: will provide comprehensive data on vessel performance, fuel consumption, and route optimization
- Advanced Sensor Systems: Opt for vessels with advanced sensor systems such as Automatic Identification Systems (AIS) and Environmental and Fuel Management Systems (EFMS).
- Data Analytics and Reporting: Incorporate vessels that offer robust data analytics and reporting capabilities. Advanced data analytics tools facilitate in-depth analysis of operational data, helping to identify trends, optimize performance, and make informed decisions. Effective reporting supports proactive management, improves transparency, and assists in optimizing maintenance and operational strategies.
Selecting the right Offshore Supply Vessel (OSV) requires careful consideration of operational needs, environmental conditions, vessel types, and technological features. You can optimize efficiency and reduce costs in demanding offshore environments by aligning these factors.
Want to learn more about the OSV Market? download our 2024 report.
Next, we’ll explore a real-world case study demonstrating how a strategic approach to vessel selection and data analysis can lead to significant operational improvements and cost savings
REAL-WORLD USE CASE:
HOW TO OPTIMIZE YOUR VESSEL’S PERFORMANCE
To demonstrate the practical application of the concepts outlined in this guide, we present a real-world case study that highlights the benefits of a structured approach to selecting and operating Offshore Supply Vessels (OSVs). In this case study, a major oil and gas operator in the North Sea needed to optimize their fleet to reduce operational costs and improve efficiency. The company faced significant challenges with one of its vessels (VESSEL A).
Understand Operational Needs and Environment:
VESSEL A operates in the challenging North Sea, dealing with harsh weather and strong currents. Its operational profile includes:
- Long Standby in the 500m Zone: Required precise positioning and stability near offshore installations.
- Transit Operations: Focused on inter-field transit, requiring reliability across varied sea states.
- Walk-to-Work Transfers: Facilitated safe personnel transfers, necessitating specialized gangway systems and high stability.
- Non-AHTS Operations: Concentrated on supply roles rather than anchor handling.
- In Port: Often on standby, highlighting the need for efficient fuel use and suitable accommodation facilities.
Know the Types of Offshore Supply Vessels:
VESSEL A is an AHTS vessel but isn’t performing typical AHTS tasks such as anchor handling or rig towing. Instead, as described above this operation profile could be more aligned with a PSV. A PSV, designed for cargo transport and personnel transfers, could be more cost-effective and better suited to these tasks.
Evaluate Vessel specifications:
VESSEL A uses a conventional propulsion system. After a detailed analysis, we determined that a diesel-electric propulsion system would be more appropriate. Diesel-electric systems offer greater fuel efficiency and operational flexibility, particularly beneficial for tasks requiring variable power output, such as standby operations and inter-field transits.
Prioritize Fuel Efficiency:
By leveraging the steps above, we created a comparative table with other types of vessels to analyze fuel efficiency possibilities comparing VESSEL A, B, and C:
VESSEL A | VESSEL B | VESSEL C | |
VESSEL TYPE | AHTS | PSV | PSV |
PROPULSION | Conventional | Diesel Electric | Diesel Electric |
POWER (kW) | 10 200 | 5 696 | 5 696 |
NB OF MAIN ENGINES | 4 | 4 | 4 |
LOA* | 73.2 | 80.4 | 80.4 |
The table highlighted significant differences in fuel consumption, particularly concerning the propulsion systems:
- VESSEL A: Conventional propulsion, 3.3m³/operational hour
- VESSEL B: Diesel-electric propulsion, 0.6m³/operational hour
- VESSEL C: Diesel-electric propulsion, 0.7m³/operational hour
These figures represent the total fuel consumption per cubic meter (m³) per operational hour, excluding standby time and transit. The analysis revealed that VESSEL A’s conventional propulsion was significantly less fuel-efficient compared to the diesel-electric systems used in VESSEL B and C.
Assess Technological Integration:
Hopefully, VESSEL A was equipped with integrated technologies that allowed us to leverage the vessel’s onboard sensors and Opsealog’s data analytics and reporting solution to address performance issues. The advanced sensor systems provided real-time data on critical parameters such as fuel consumption, engine efficiency, etc…While Opsealog’s solutions Marinsights & Streamlog played a pivotal role in processing and interpreting this data. We were able to diagnose the root causes of performance issues and develop targeted recommendations based on data-driven insights:
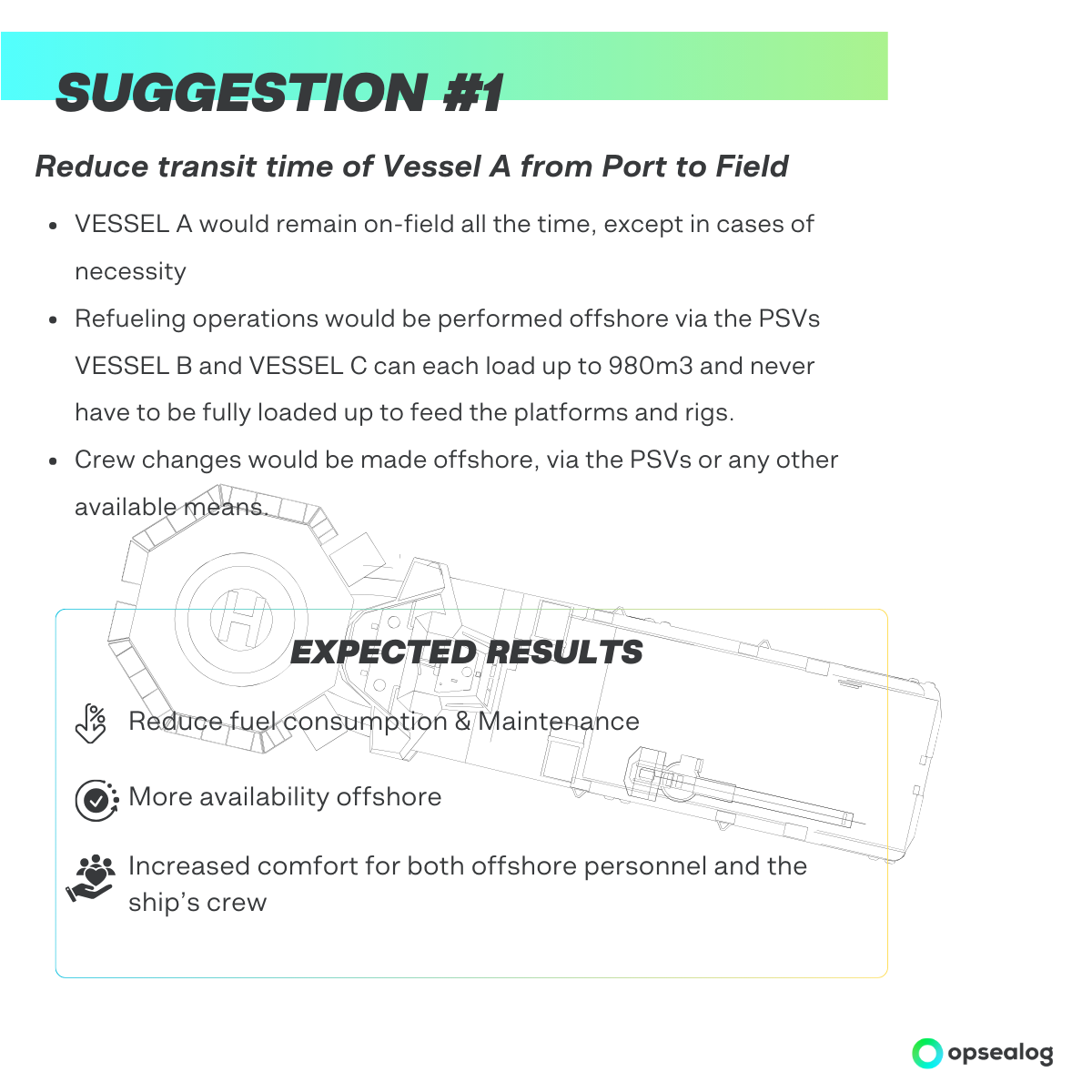
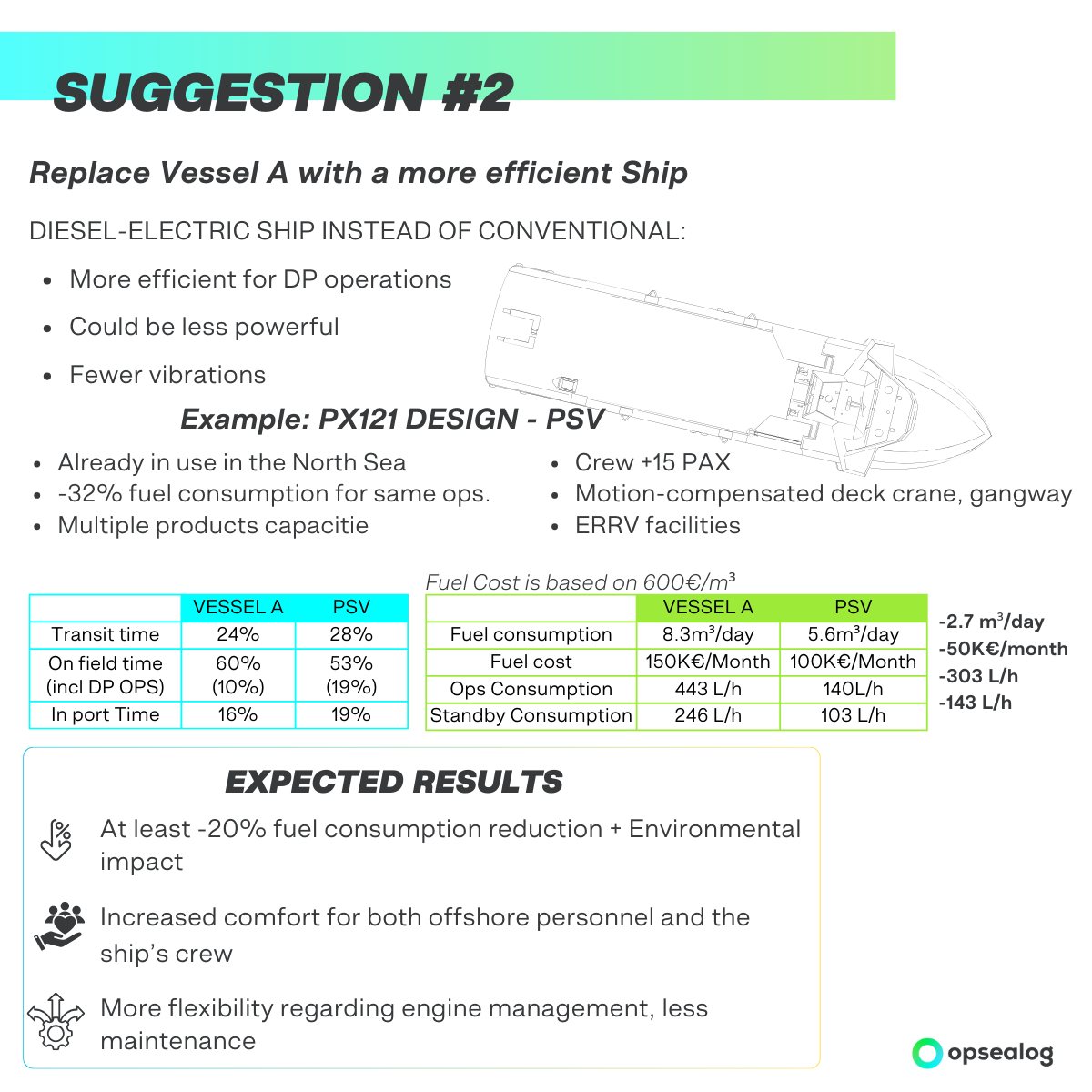
Conclusion
Optimizing fleet performance requires a strategic approach that leverages data analytics, informed decision-making, and continuous performance assessment. By implementing these strategies, operators can achieve significant cost savings, improve operational efficiency, and reduce their environmental impact. Data analysis can help determine if the different performance clauses defined in charter party agreements (fuel performance, maintenance, crew management, requirements, etc.) have been met. Bringing the owner and charterer on the same page with a common digital base can help determine if a vessel is having abnormal fuel consumption due to operational practices or a technical or maintenance problem, for example.